Spezielle Vorrichtung zur Materialprüfung gibt es bundesweit nur an ganz wenigen Hochschulen
(wS/uni) Siegen – Die Universität Siegen hat in Eigenregie einen Hopkinson-Bar – einen hoch spezialisierten Versuchsstand zur Materialprüfung – gebaut. Wissenschaftler, Studierende und Mitarbeiter der mechanischen Werkstatt der Universität arbeiteten gemeinsam an der etwa zehn Meter langen Vorrichtung, die es in dieser Größe bundesweit nur an ganz wenigen Hochschulen und Instituten gibt. Das Besondere: Der Hopkinson-Bar ermittelt Materialeigenschaften unter dynamischen Bedingungen. Das Gerät misst, wie stark sich Bauteile oder Materialkomponenten unter schneller Belastung verformen. Für die Forschung im Department Maschinenbau, Lehrstuhl Festkörpermechanik, ist das im wahrsten Sinne des Wortes von elementarer Bedeutung.
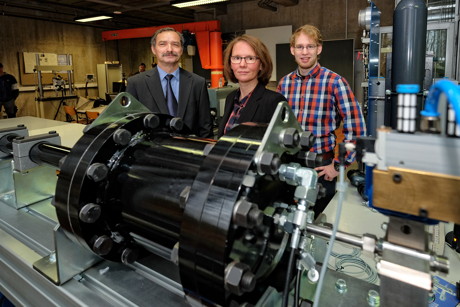
Einen Hopkinson-Bar zu kaufen, wäre ein unrealistischer Wunsch gewesen. „Das hätte die Universität mehrere Hunderttausend Euro gekostet“, sagt Dr. Ralf Nötzel, der deshalb vor zwei Jahren vorschlug, die komplexe Prüfanlage selbst zu bauen. Prof. Dr.-Ing. Kerstin Weinberg, Leiterin des Lehrstuhls Festkörpermechanik und Dr. Nötzel als wissenschaftlicher Mitarbeiter wagten das Projekt. „Das notwendige Wissen ist ja vorhanden und die handwerklichen Voraussetzungen ebenfalls“, erklärt Prof. Weinberg. Wissenschaftler, Studierende und Techniker der Uni-Werkstatt arbeiteten dabei Hand in Hand. Der Hopkinson-Bar ist die bislang größte Konstruktion, die je in der Uni-Werkstatt entstanden ist, sagt Werkstattleiter Friedhelm Stahl, der die Zusammenarbeit der Theoretiker und Praktiker lobt.
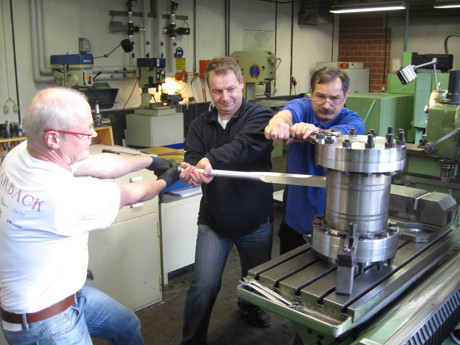
Die glänzende, zweiteilige Metallstange auf dem massiven Unterbau erinnert ein bisschen an einen Schwebebalken. Die Konstruktion nimmt die gesamte Breite des Labors des Lehrstuhls Festkörpermechanik am Paul-Bonatz-Campus
ein. Der Vergleich mit dem Schwebebalken ist gar nicht so weit weg. Denn die beiden 60 Kilogramm schweren Metallstangen „schweben“ tatsächlich auf einem Druckluftpolster. Eine Lösung, die Daniel Kowalski im Rahmen seiner Bachelorarbeit entwickelt hat. Um genaue Messergebnisse zu bekommen, soll die Stange durch möglichst wenig Reibung gebremst werden. Kommt sie erst ans Laufen, wirken Kräfte, bei denen man um die Wand zum Nachbarraum bangen muss. „Aber keine Sorge“, so Nötzel, „das ist alles genau berechnet und vom TÜV geprüft.“ Die größte Herausforderung beim Bau der Prüfmaschine war der Hochdruckkompressor, der als einziges Teil außer Haus gefertigt wurde. „Die sicherheitstechnischen Vorschriften sind da enorm groß“, so Prof. Weinberg.
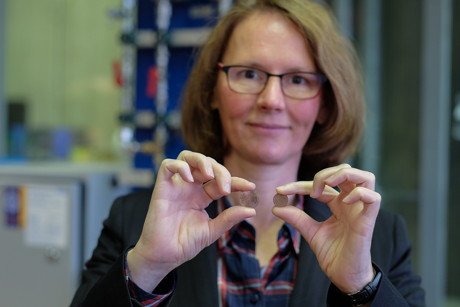
Dass der selbstgebaute Hopkinson-Bar funktioniert, zeigen Prof. Dr.Weinberg und Dr. Nötzel am Beispiel einer 1-Cent-Münze. Der Hochdruckkompressor wird eingeschaltet und erfüllt die Werkstatt mit einem satten Geräuschpegel. „Es wird noch lauter“, warnt Nötzel. Genau dann nämlich, wenn der Schieber geöffnet und das durch die Druckluft beschleunigte Projektil auf den ersten Teil der Stange trifft. In diesem Fall mit über 100 Metern pro Sekunde. Höhere Geschwindigkeiten sind möglich. Mit einem lauten „Plong“ treffen die beiden Stangen aufeinander, und mit einem leisen „Pling“ landet das Cent-Stück auf dem Laborboden. Der Stoßimpuls hat gereicht, um die Münze ordentlich zu plätten und durch die Luft zu wirbeln.
„Metalle sind ja in der Regel gut durchgeprüft“, erklärt Prof. Weinberg. „Interessant sind zum Beispiel die Eigenschaften von Kunststoffen, aber auch biologischem Gewebe.“ Dabei geht es nicht um Crash-Tests im üblichen Sinn. „Wir wollen klären, was passiert, wenn Menschen einer starken Druckluftwelle ausgesetzt sind. Was richten die Kräfte innerhalb des Körpers an?“, erklärt Prof. Weinberg. „Dazu brauchen wir Materialdaten. Wir werden in der nächsten Zeit sehen, was das Gerät alles kann.“ Die seltene Prüfmaschine, die die Universität Siegen nun vorhält, kann im Rahmen von Forschungsaufträgen auch gern von interessierten Unternehmen genutzt werden.
Wie funktioniert ein Hopkinson-Bar?
Eine Probe des zu untersuchenden Materials wird zwischen zwei Metallstäben eingespannt – dem Eingangs- und dem Ausgangsstab. Ein so genannter Striker, in diesem Fall ein durch Druckluft beschleunigtes Stahlprojektil, trifft auf den Eingangsstab und verursacht dort einen Stoßimpuls. Dieser Impuls läuft durch den ersten Stab und wird zum Teil am Stabende reflektiert, der andere Teil setzt sich durch die Materialprobe hindurch in den Ausgangsstab fort. Die Änderung der Impulse wird gemessen und gibt Auskunft über die Eigenschaften der Materialprobe.
Fotos: Uni Siegen
.
Anzeige/Werbung – Jetzt clever werben bei wirSiegen.de – Infos hier
[adrotate group=“3″]